Sorty was born at the intersection of sustainability and business value. After winning PennApps XVI and garnering a finalist performance at Facebook Hacks, we knew we had an innovative idea.
Our initial prototype—a version capable of sorting one item at a time—was created out of a borrowed plastic waste bin, cardboard, and some motors we found lying around. The latest iteration is a pick-and-place machine that can handle multiple objects, first identifying and separating recyclables, then discarding the remaining items into a distinct waste compartment.
The process for designing and building the latest prototype was an iterative one. We thought about how we might technologically solve the mechanical task of picking up and throwing objects away, a challenge that has typically been solved using a 6-DOF (degree-of-freedom) robotic arm. However, training a machine learning algorithm to pick up randomly-sized items of any orientation seemed like a daunting task. Existing hardware would have been prone to constant malfunctions and would have also become too costly, diminishing our value proposition.
How might a system be capable of physically picking up, pushing around, or otherwise manipulating individual objects to get them from one location to another?
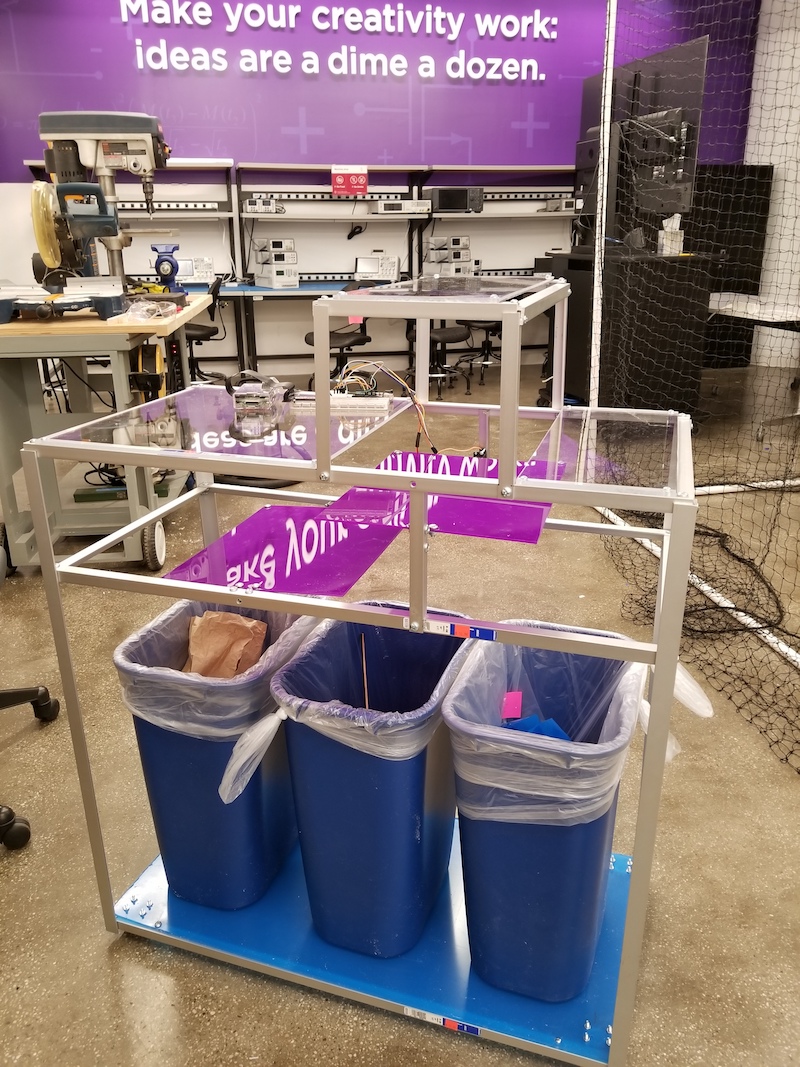
The Prototyping Fund supported Sorty in iterating their product design to this Minimum Viable Product.
We considered using a combination of tools such as an electromagnet for ferrous materials and a suction or gripper for non-metallic items. We also had to think about integrating the hardware with our Python-driven software, so the system would know when to move the X and Y axis to a specific coordinate in the bin. While visiting the NYU Tandon MakerSpace, our teammate, Kevin Nguyen, found inspiration when watching the 3D printers in action. He proposed using a system of motors configured in a way similar to how 3D printers, laser cutters, and other CNC machines are designed. This vision led to our latest prototype, which is essentially a CNC machine mounted on top of a large box with a moving platform. The platform-based structure is a derivative of our initial model and is a design we believe simplifies the technological demands of our MVP.
During the iterative process of prototyping, you can build a “looks-like” design prototype, a “works-like” functional prototype, or both. While developing our MVP, we taught ourselves mechatronics engineering and the software languages necessary to implement its tools. In the future, lower cost electrical components purchased at scale will enable us to reduce the per unit costs of each Sorty bin.
The NYU Prototyping Fund has afforded us the resources and budget to follow the natural prototyping life cycle necessary to bring our MVP vision to reality. Without the coaching sessions that helped guide our customer discovery process, which in turn shaped our prototyping milestones, we would be stages behind our current position.
In private, we like to call our team the Super NYU team. We have student entrepreneurs from four different NYU schools! The teammates are Earl Co (Tandon BS '16), Mohammed Yassen (Stern MBA '19), Rishub Nahar (Courant + Stern BS '21), and Kevin Van Nguyen (Wagner MPA '16).
Meet the Sorty team in person at the NYU Prototyping Fund Showcase on Tuesday, May 1!